3DADEPT Media: Thermwood @ RAPID+TCT 2024: Broadening the scope of possibility for Large-Scale Additive (and Subtractive) Manufacturing
https://3dadept.com/thermwood-rapidtct-2024-broadening-the-scope-of-possibility-for-large-scale-additive-and-subtractive-manufacturing/
Thermwood @ RAPID+TCT 2024: Broadening the scope of possibility for Large-Scale Additive (and Subtractive) Manufacturing
Starting from roots of thermal coatings & woodworking, morphing into an industry-leading CNC machine tool OEM, and a few years ago bridging into the Additive Manufacturing space; the Thermwood group had a multi-faceted presence at this year’s RAPID+TCT show. “We’re showing the end-to-end solutions we offer, especially for fixturing and tooling that’s either printed or machined,” Brent East, US Account Manager for Thermwood explains. At their front-row RAPID+TCT booth, there was a demo station for their new Cut Layer Additive system, along with an array of different examples of tooling for composite layups, thermoforming molds, and enclave fixtures for baking aerospace-grade components. That, along with some of the friendliest exhibitors at the show made for an excellent experience learning about the latest & greatest with this reputable machine tool OEM and CAD/CAM software partner.From humble roots as a contract manufacturer
In the early years of Thermwood, the team started as a job shop for tooling & fixtures for thermoforming and woodworking applications. The expertise derived from the company’s knowledge in the CNC machining industry still remains a core element of the organization today. This spawned a new era for the group as they began to evolve, where they envisioned a product to bring to market. The accumulated expertise as a manufacturer proved to be vital when the group began to develop their own line of CNC Gantry Systems tailored for woodworking; some of the first to enter the market in the early 1970’s.To the emergence of Cut Center for traditional CNC routers
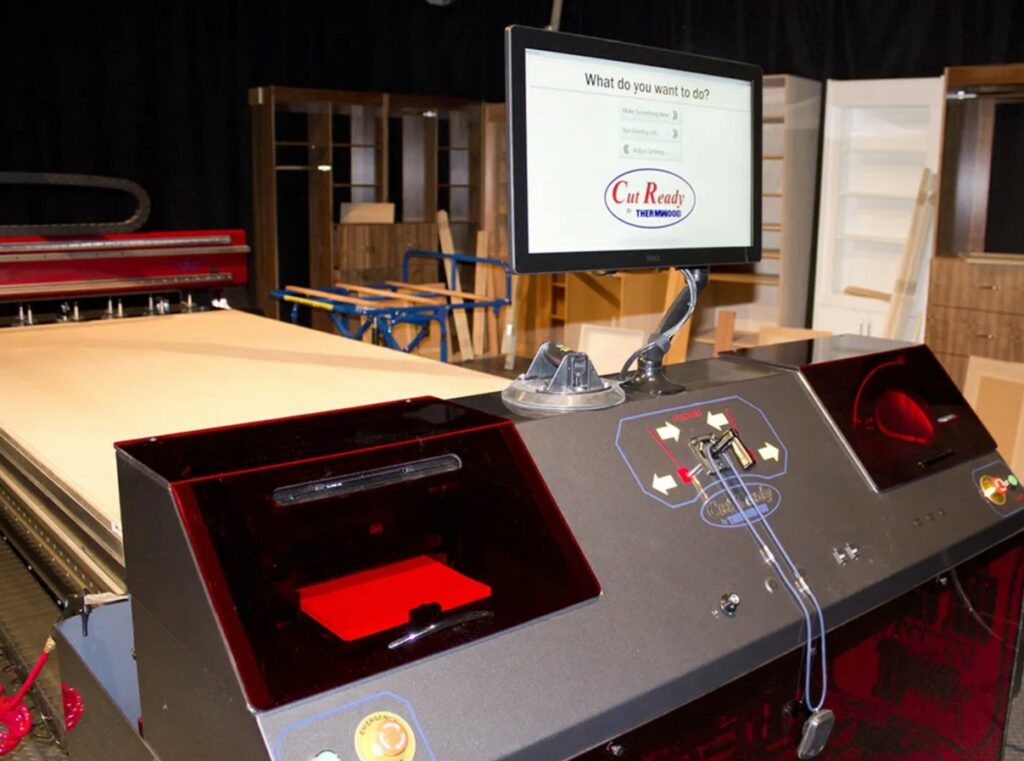
Building off that in the Additive Manufacturing space
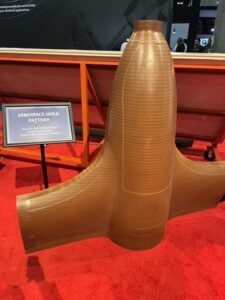
While recently launching a SaaS product for automating CAM in 3D printing
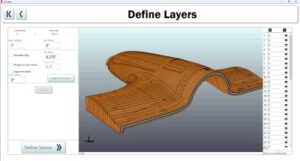
Why Cut Layer Additive matters for manufacturers
There are a number of occasions when you want to make a large part, but don’t want to machine away a bunch of material to cause waste and minimize profit. “Simply inputting your material & wall thickness (as shown in software illustration above) is all that’s needed to produce the CAM for any large-format 3D printer. The built-in machine learning allows for routing things like dowel pins and other common ways to assemble a large part that’s printed (or machined) in multiple pieces,” Wilmes says. “What’s usually taking a skilled CAM programmer weeks to program can happen in a matter of hours with very few inputs from the user.” There’s no expensive hardware to run Cut Layer, computing can be done at the machine or offline, and inputting the CAM file into a Thermwood machine will have you printing (or cutting) in fairly little time. That’s the power of Cut-Layer, its embedded machine learning algorithm which makes manufacturing a large-format part much easier than hand-calculating, CAD model manipulation, mapping the toolpaths manually, and so many other tedious time-consuming tasks.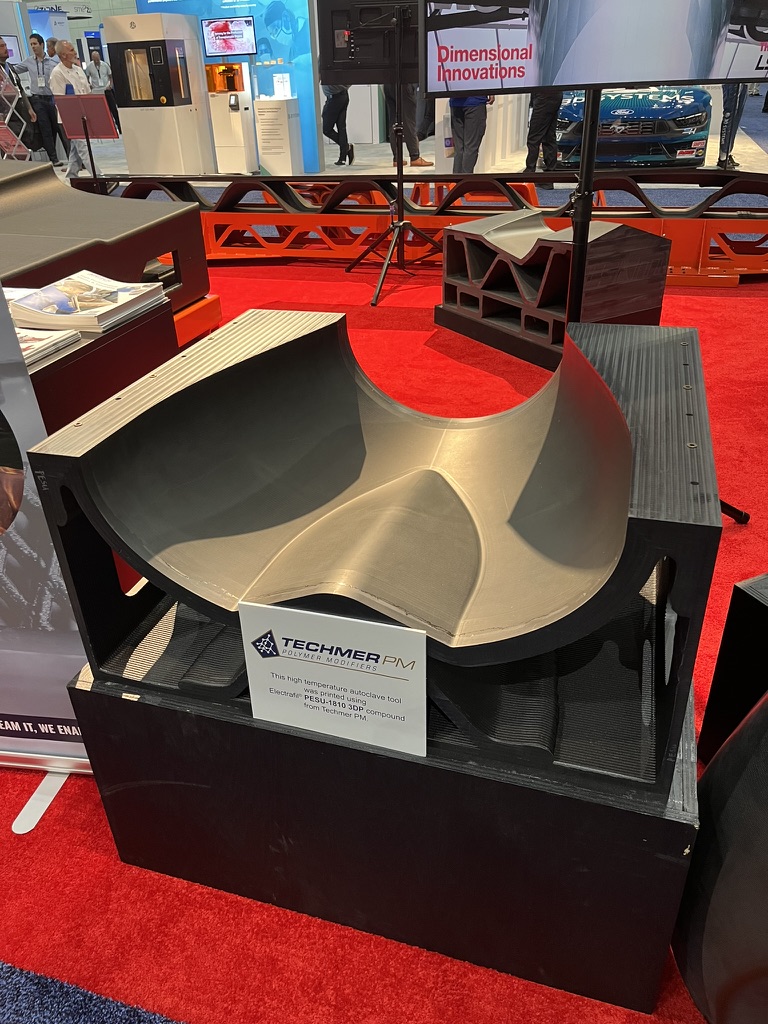
Additive solutions showcased at RAPID+TCT 2024
At the RAPID+TCT show, Brent East walked me through some of the various tooling examples they had on display. “On the Additive side, we’re featuring large scale tooling for composite layups as well as fixturing to take the final tool to production. In talking with vendors at RAPID, we’re seeing an uptick in material advancements which we’re adapting to on the machine side of things to stay current with the latest in polymer technology.” In walking the show at RAPID, this uptick in material science was evident on all levels of the spectrum. Whether it was at the consumer level with polymer companies like Polymaker branching into metal powders from Linde, along with carbon fiber and other composite filament manufacturers. Read more about the RAPID+TCT show overview here. East went on to talk about some of the recent expansions in the space industry along with home-building: “With all of the investments in R&D that are made on the polymer side, it’s typical for hardware OEMs like us to adapt to that newer, faster polymer on the market and build machines to utilize that.” The group is also noticing a large displacement in the casting and foundry industry as well, with end-users looking towards Large-Scale Additive as a solution for shorter lead times and lower costs, as long as the production volume allows for the economies of scale. Aluminum tooling is another area this group has extensive experience in, which was clearly demonstrated at RAPID.Innovations to expect from Cut-Layer Additive & beyond
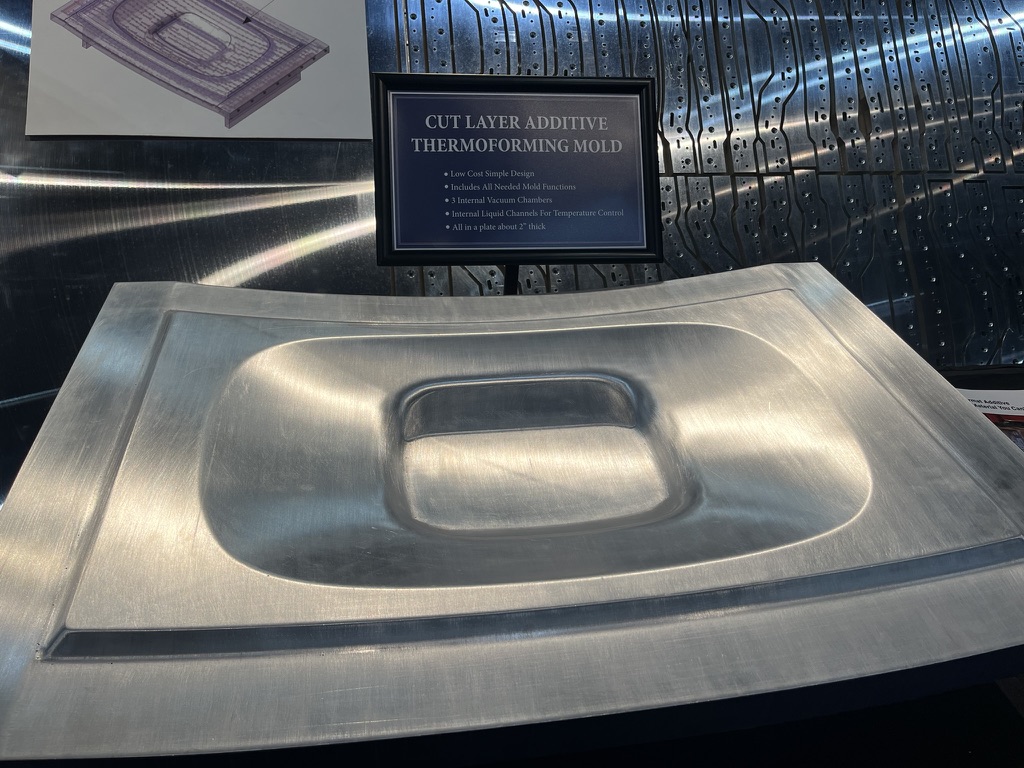