3DADEPT Media – RAPID+TCT 2024: Hollywood meets Additive Manufacturing
https://3dadept.com/rapidtct-2024-hollywood-meets-additive-manufacturing/
RAPID+TCT 2024: Hollywood meets Additive Manufacturing
With over 400+ exhibitors, 200+ conference speakers including 125 educational hours of industry-leading presenters, and 100,000+ attendees, this year’s RAPID + TCT show was a highly anticipated event. With California as a whole being the largest manufacturing producer in the United States, there were a multitude of West Coast small businesses, students, scientists, innovators, makers, and general 3D Printing nerds alike all centered in the City of Angels to learn about the latest technology in the Additive Manufacturing space. Familiar groups like Women in 3D Printing, Stratasys and the 3D Printing Nerd all hosted fun, rooftop karaoke sessions and happy hours following the first few nights of the conference. There was a noticeable increase in presence from Asian manufacturers as well, given the proximity to Eastern countries for overseas exporting. Additionally, the influence of Hollywood and the film industry was on full display, with a variety of booths and showcases displaying movie props, figurines, and full life-sized prints for recognizable American pop culture references throughout the conference halls.
Faster, smarter more affordable, desktop 3D printers
A decade ago when Netflix launched the 3D printing documentary “Print the Legend”, Desktop 3D printers were thought of as nothing more than an inexpensive means to produce plastic prototypes. Fast forward to 2024, and we now have a large emergence of Desktop 3D printing companies producing quality products for the casual hobbyist all the way up to Fortune 500 Design & Engineering companies – with machines becoming faster, quieter, more affordable, and a wider envelope of material selection. Companies like Bambu have gained a ton of momentum in more recent years, especially within the maker and retail consumer market. This year, Bambu and a variety of other maker-centric brands with large show presence in heavily-trafficked areas ambition to cater to the masses that were in attendance.
Volume production Additive Manufacturing (Colibrium)
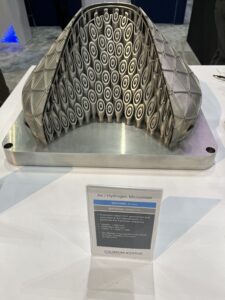
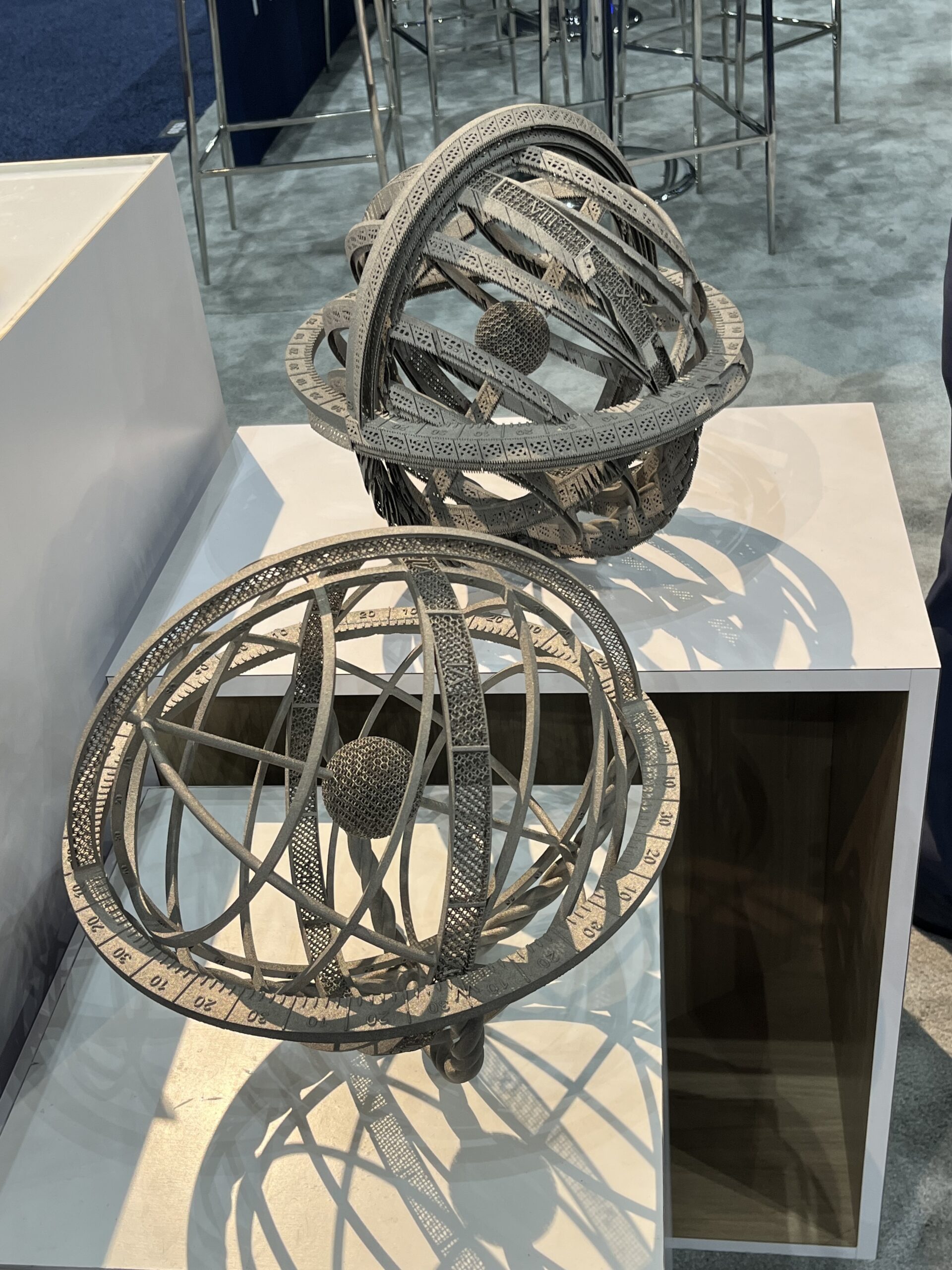
Continued expansion of materials (Lithoz)
Ceramic 3D printing was once a far off thought, but is now being brought fruition in the Additive community with advancements in hardware and material technology. Initially AM was used only with cheaper polymer materials such as PLA, ABS, and ASA. As the technology became widely adopted, came the emergence of Metal 3D printing with powder-bed and laser-sintering technologies. The next giant leap in material science with 3D printing is likely in the realm of being able to additively manufacture high quality ceramic components. Norbert Gall of Lithoz explains “Ceramics is the next step in the Additive Manufacturing revolution. It offers immense control under extremely hot and cold conditions, while maintaining part resolution and fine features for a variety of applications and component sizes.” Lithoz showcased a very large, circular part (as shown below) which was all printed in one batch.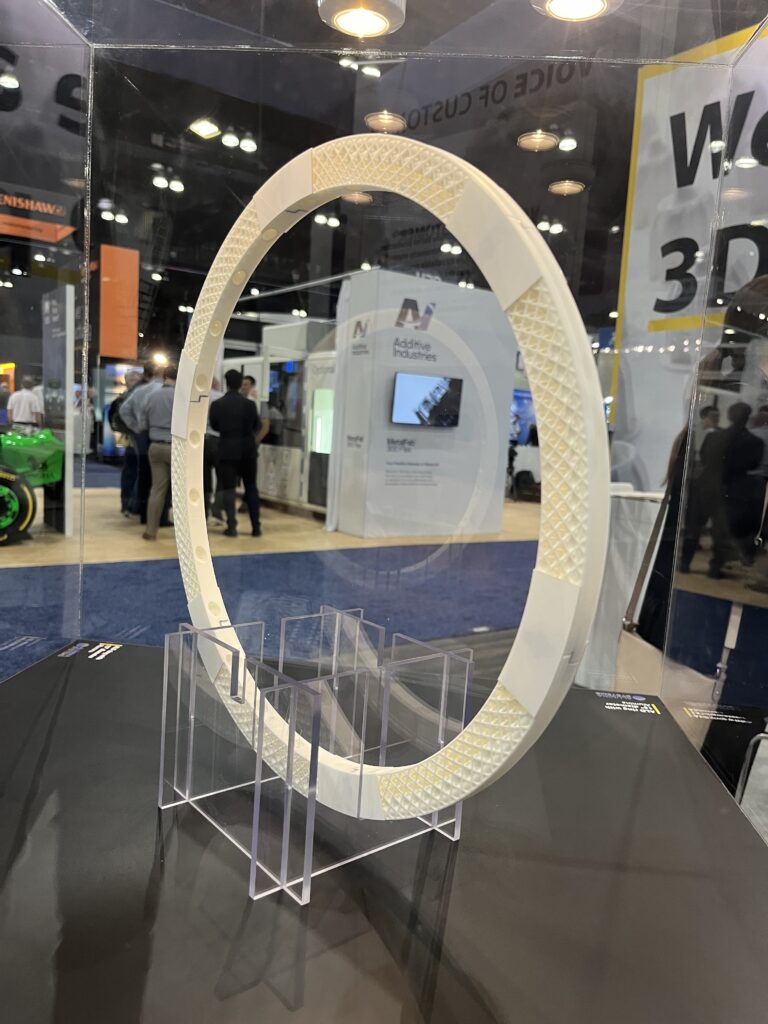

Quality / Traceability (Phase3D)

Increased attention on post-processing capabilities
While the dream of AMis simply loading a CAD file and just pressing go, the reality is that there’s often a much needed intervention of post-processing and after-print treatment that’s involved for the majority of 3D prints. Organizationslike Solukon are addressing just that with their automated depowdering systems. Marina Haugg of Solukon was at the booth this year showcasing the SFM-AT1000-S; a large format automatic depowdering system for parts of up to 1,000mm and 800kg. “While many focus on all of the features & capabilities of the 3D printers themselves, it’s crucial to not forget about the post-secondary operations that are done post-print,” Haugg explains. “Our systems are geared towards OEM’s and end- users in a high-volume production environment and are looking to automate the way they handle metal (and plastic) components once they’re off the print bed.”
Star of the show (nTop + Cobra Golf)
Without a doubt, the busiest attraction and eye-catching demo had to be the metal 3D printed golf irons designed using nTop software in collaboration with San Diego-based Cobra Golf. Ryan Roach of Cobra headed up the design innovation that is taking the golf industry by storm through the help of nTop’s AI-enabled topology optimization design & analysis software. Allowing for variable wall thickness, hollow internal channels, and complete customization; Roach explained the design thought-process in a keynote presentation on Day 2 of the show. nTop’s CAE software has been utilized in industries beyond golf, spanning heavily into aerospace for heat exchangers, and other commonly 3D printed components for rockets, aviation, and more.