Why CNC Machining?
Since the dawn of the US Industrial Revolution, conventional machining has become the “original” way to form metal into precise parts and geometries. Metal cutting machines served as a total means to production for the American labor force, especially at the height of both World War’s. Manual milling machines and manual engine lathes soon sprung up around military, tool & die, automotive, aerospace, and other various shops throughout the US. This immense exposure and adoption of machining allowed for growth and innovation by an array of institutions across the country. This was at a time where 4-year degrees were not heavily marketed, resulting in a large amount of high school graduates to get involved in trades such as machining or welding. With accelerated apprenticeships and journeyman machinist programs, it didn’t take long for a novice to learn the ways of machining with some engineering know-how and steady hands/eyes. With a huge swarm of new engineers and manufacturers it allowed for ramped production, resulting in immense growth of endless industrial sectors of the economy.
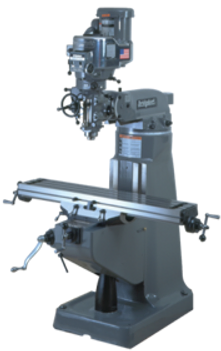
Born in the 1940’s, the Bridgeport milling machine (pictured) served as the benchmark for manual milling machines, boasting a robust 3 axis setup that was able to cut a wide variety of metal parts. A lathe is a 2-axis machine that handled most cylindrical/round parts from piston heads to gun barrels, to screws and so much more. Milling machines combined with manual engine lathes was the bread and butter combo for machinist’ alike. A skilled craftsman was able to produce parts by cranking the handwheels on these machines, manually engaging the cutter with the raw material. In the early stages of innovation, knee mills would often be “retrofitted” to accommodate a CNC control, much like that of a ProtoTRAK retrofit. Now a computer is telling the machine where to move instead of the hands of a machinist, further automating the machining process.
With the implementation of computers into the mix, CNC
machines have now become the automated version of a once slow, labor intensive practice. As the years progressed, computers slowly began tapping into the manufacturing space, allowing the shop owner to do much more work with far less labor. Through computer generated codes known as “G-Codes,” a set of precise data points and commands are read by the machine, and performed automatically, thus moving the machine to specified dimensions to remove metal from the workpiece. No longer did the operator need to manually move the machine, it is now entirely controlled by way of computer operation. Soon after CNC was introduced, machine tool manufacturers around world began to develop their own machines that could accommodate a wide variety of operations. From multi axis CNC milling, to multi spindle CNC turning, and so much more….technology began to change the entire game of machining and challenged shops to adopt and implement these new methodologies.

The overwhelming theme to sustainability for most machine shops today is to do more work with less labor. As mentioned in Drew Desilver’s article, the US manufacturing job market has been on a decline, while output has risen significantly thanks to conveyor systems, robotics, and many other automated processes. In today’s machine shop, there is a vast sophistication of milling and turning equipment available to shop owners for a multitude of materials. A 5-axis machining center is a piece of CNC machinery that pops up in a lot of different shops today, allowing for a part to be machined with very little to no secondary machining needed afterwards. With automated pallet changing systems, production CNC machines can often be set up to run jobs overnight by way of “lights out machining.” Robotics is just another piece of technology that rapidly advances the possibilities of automation within any working environment.
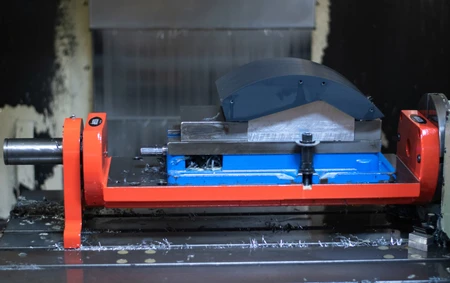
In a lot of senses, the majority of machines shops today have the challenge to do more with less. More skillsets within selected employees, more capacity within certain machines, more utilization of time spent designing work in a CAD software, and so much more. Although there is argument that automation/robotics will render future workers useless, there is much opportunity to advance and adapt along with technology. Machining is just one example of the many other wickedly efficient technologies that will not stop evolving and adapting to newer and better systems/processes. With a shortage of skilled workers in the manufacturing industry, it has never been a better time to look into becoming a machinist.
CNC is a topic I will touch on multiple content pieces moving forward, feel free to reach out with any content ideas/projects you are currently working on!