Returning Where It All Started: Martin Manufacturing (Trunnion Table)
It wasn’t until my junior year of undergrad that I first learned about the fascinating world of industrial manufacturing at an internship with Martin Manufacturing in Elsmere, Kentucky. What once started out as a pain point for Stan’s machine shop, slowly became a technology that he would later go on to start his own business with. From humble “garage startup” roots to a thriving business of 25+ years, Martin Manufacturing has had much success with their line of 4th Axis Trunnion Tables/Workholding solutions. “Manufacturing” and “efficiency” are two words that run parallel to one another in a high pressure, industrial environment. Shops everywhere are constantly obsessing over perfection, under pressure to maximize their resources to deliver precision parts in a timely manner. A trunnion is just one of the many methods to producing complex, machined parts in a fast, and productive manner.
Essentially, a trunnion table is a workholding accessory that comes in various sizes and platforms, allowing the operator to clamp a part to the table and machine up to 3 sides of that part in one setup. (See video here for demonstration) These versatile tables can be used on a variety of milling machines, and are a bolt-on accessory for a range of 4th axis rotary tables on the market today. To produce a part on a standard Bridgeport knee mill, the operator is forced to keep readjusting the position of the metal part after each side of the raw material is cut to a precise dimension. Often times this part is held in a vise mounted to the milling table, which has to be manually opened and closed when the raw metal stock is flipped. Fast forward a few decades, and the operator is now capable of not having to handle that part over and over again by way of automation and modern machining capabilities. When an operator is simply able to hit the “start” button and not worry about manually handling that part, it frees them up to other tasks such as running other machines, doing secondary work on a part, or prepping jobs to later be machined. Hydraulic fixtures, pneumatic spindle brakes,

and elaborate clamping systems are just a few other devices that help production machine shops improve the accuracy and precision of their work. Now less labor is required to run more machines, having a dramatic impact on the productivity and profitability of that shop.
In the early 90’s Stan ran a job shop running mills, lathes, doing programming, performing secondary operations, and just about everything that one could possibly do in a machine shop. “I had so many jobs that were timely and costly because we kept having to unclamp parts to re position them for the next
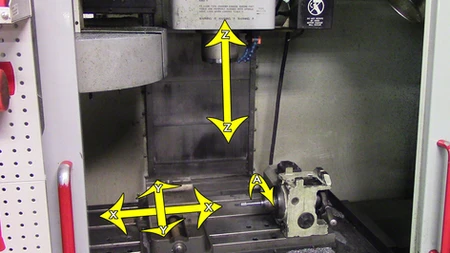
operation,” Stan remarked. “I just knew there had to be some way to make these setups more efficient.” Overtime, Stan gathered enough knowledge of machining to develop his own blueprints to then make a prototype device in his dad’s garage. It was there that Stan gathered the idea for the product that is now the cornerstone of his business today; the Trunnion Table. Though plenty of people were rigging up their own homemade trunnions, no one was actively marketing it as a product. He first began to run jobs with vise fixtures mounted to a Haas rotary table (see below), which allowed his Vertical Mill (VMC) to run like a Horizontal mill (HMC) thanks to the Trunnion’s 270 degrees of travel in the A-Axis (see diagram above for an illustration)

of the table. “After using my trunnion, the least profitable jobs became my most efficient and high ROI jobs,” said Stan. With continuous design improvements and rigorous testing, he was able to perfect his Trunnion overtime, through many different applications and design iterations along the way. “Once we got an understanding of all that this table was capable of, we started making more and using them as our go-to workholding solution for most milling work we did,” said Stan. “It wasn’t soon after that we saw a real demand for this type of product.”
Today, Stan runs his family owned business with his wife Toni, and son Michael along with a team of machinists, programmers, and other well-rounded engineers. Aside from his main product line, his crew is dedicated to utilizing their own technology for what truly it’s meant to do…cutting parts! Their CNC

job shop is running production jobs for automotive, motorcycle, aerospace, and various other industries…all that are typically prepared on a trunnion setup. There is also a sense of partnership ingrained throughout the organization from the relationships they have managed to build with distributors nationwide. “We wouldn’t have grown and learned what we know today if it weren’t for the rotary table
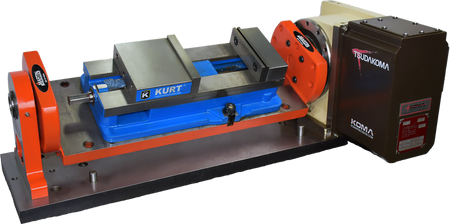
manufacturers we partner with to deliver quality to their end users. At the end of the day that’s their goal…satisfying customers, and enabling them to produce success in their own business,” remarked Stan on a recent #MakingChips podcast. Different applications with distributors such
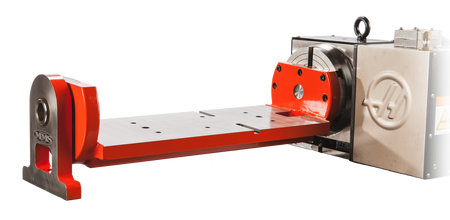
as: Haas, Lyndex Nikken, and Koma Precision has enabled an increased effort to improve and further innovate the capabilities of a Trunnion. “We are able to provide complete turnkey packages for our customers to get up and running,” said Stan. “With the help from our partners, we are able to be on completely new levels of engineering/technical know-how with a team of dedicated engineers for just about any type of job.”
One of the themes of conversation I heard overwhelmingly when meeting with Stan was the need for young, motivated individuals that are willing to learn the industry and grow with it. “Not only finding good employees, but people that are invested in the core culture, and people that can come in and quickly adapt to this kind of fast paced environment,” Stan remarked. Michael, Stan’s son, has taken a role as the marketing/creative content side of Martin Manufacturing for the last two years. SolidWorks programmer and machinist Ryan has able to learn the ins and outs of a machine shop through a unique apprenticeship with Stan and senior engineer/toolmaker Chuck. “The future of this industry is indicative on the interest and innovation from the younger audience,” said Stan. “The sophistication of technology does not stop, and there is such a need for young, tech-savy minds to be able to come in and pick up where the older generation left off.”
Apprenticeships are just one of the many ways that companies across the nation are using to adapt young talent into these highly skilled, technical roles. In college you are paying money for a non-revenue producing activity, whereas apprenticeships are often paying an individual to learn a skill or trade. As the speed that technology can be adapted/implemented expands, the possibilities for young inventors and entrepreneurs is seemingly endless. I am absolutely optimistic and ambitious with the opportunities that are out there for those with a can-do attitude and an impeccable work ethic. If you are reading this and want to know what the first step is, I implore you to reach out to me, I am ready and eager to help you in your journey!