6 Key Themes & Take-Away’s from IMTS 2022 (Chicago, IL USA)
After 4 long, isolating and truly strange years, IMTS was back and in full swing after being absent in 2020 for COVID-related reasons. I was fortunate enough to have an entire day to explore the 1300+ exhibitors in the over 1.3 Million square feet of space at the McCormick Center in Chicago, Illinois. With so many exhibitors and conferences packed into IMTS, I planned by day and set out to Chicago. Here are among just some of the trends and major themes I saw during my time in the Windy City:
Automation, Automation, Automation!
- Robotics, PLC’s, IOT Hardware, Smart-Connected Machinery and more were among some of the constant reminders for where Automation Technology is in the world. Programming these autonomous systems is seemingly becoming easier over the years, and smart-sensors are now widely available for shops to closely monitor vital aspects of their production facility and equipment. I’m also seeing more and more factory-floor automation these days, as companies of all sizes aim to do more with less, and increase shop efficiency.
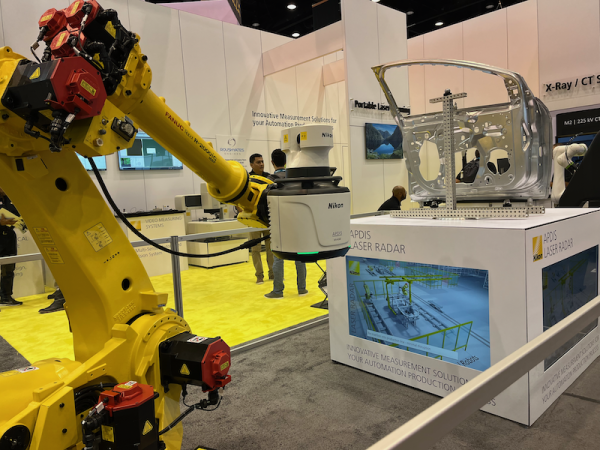
Increased Investment from Nikon in the Additive Manufacturing & Robotics Sectors
3D Printing for Production
- This is my 3rd IMTS, and throughout the years, I’ve seen a continually expanding Additive Manufacturing Pavilion in the West Hall of McCormick Place. After many years of overcoming the initial “hype phase,” I am seeing true end-use applications for 3D Printing with both Metallics and Polymers, that much was reflected in the booths of all 3D Printing Exhibitors I saw while walking the aisles. Whether it’s tooling for initial prototyping, doing small lot runs of an initial concept, or doing full-blown production with Additive, it’s here to stay, and is proving itself to be a viable manufacturing solution. It’s exciting to see a variety of large corporations make significant investments into Additive for Fortune 500, combined with Venture Capital funds allocated towards US-based startups.
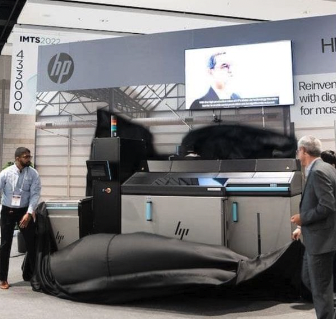
HP Announces new Metal SJ100 Series of Powder-Bed Additive Manufacturing Systems
Continuous Evolution of Machine Tools
- The South Hall (Largest Hall at IMTS) has always boasted an impressive scale of the world’s largest Machine Tool companies, along with millions of pounds of sophisticated machinery. While the CNC & Machine Tool industry has had a number of decades to mature, there is still much innovation taking place for a variety of Machinery and Equipment OEM’s across the globe. Combined with cutting edge metal cutting tools and software to fine tune predictability with CAD and CAM, the Machine Tool industry continues to evolve into a highly automated, precise means towards high-volume production.
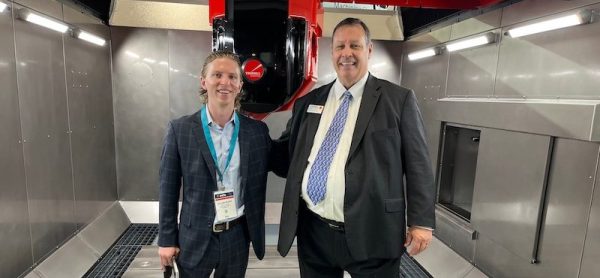
Enhanced Tooling/Workholding for Additive & Subtractive Manufacturing
- Long gone are the days where machinists use simple 3-Jaw Chucks or Manual Vises for Machining applications. Tooling & Fixturing is now to a point where Programmers, Designers & Machinists can work in true harmony thanks to innovations in design & capabilities thanks to today’s workholding companies. Additionally, new ways to make tooling, suchas Additive Manufacturing, are breaking down the barriers for traditional tooling design.
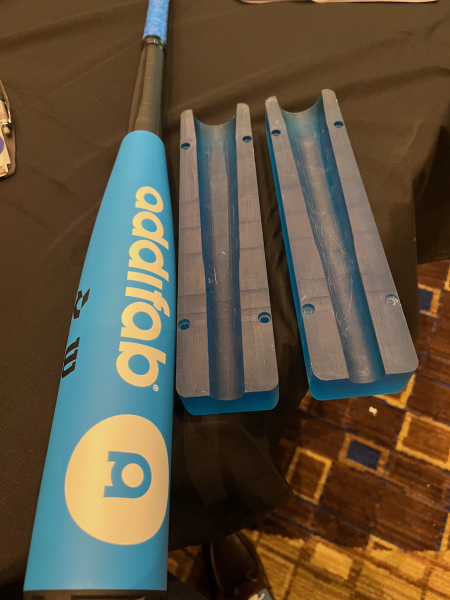
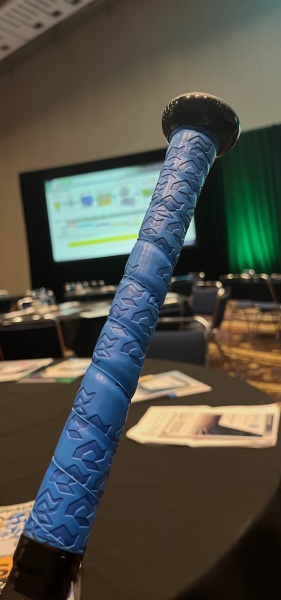
Unique Use-Cases for Robotics
- Although the US is considered a laggard in the robotics space, I was pleased to see an immense presence of robotics for a wide array of creative real-world applications at IMTS. Anything from simple machine tending and parts changing, all the way up to ambidextrous multi-task systems capable of various shop floor operations, robots and cobots sprawled the McCormick Place at every turn. A number of robots also assist with warehouse supervision, raw material packaging/delivery, and other repetitive jobs to free up human workers for more productive tasks. Though we are likely several decades out from complete robot takeover, there were certainly a higher number of these mechatronics at IMTS, and a wider array of tasks that they’re now capable of completing.
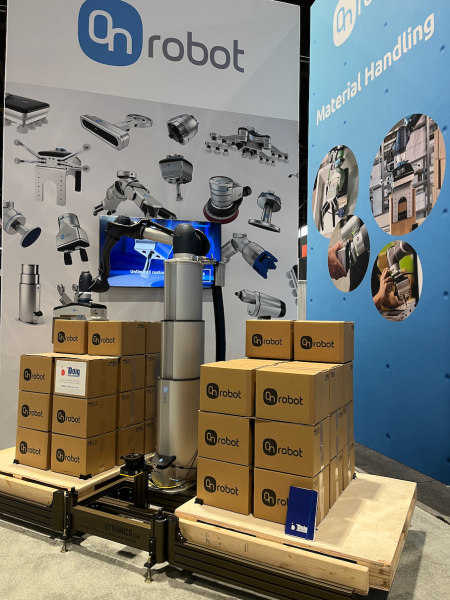
OnRobot developed robotics specifically aimed at warehouse/factory floor automation
Ever-Growing Use Cases for Industrial Software
- As computers have grown & adapted the way we live our lives, so too has the app-based software that has supported this digital transition. Strolling through the North Hall of the exhibitors, I saw a large presence of several ERP, PDM/PLM, CAD & CAM companies that have expanded their presence along with market share in more recent years. Though not all of these different software’s might not work in complete unison yet, there seemed to be a variety of 3rd party integrators present at the show to act as the “glue” to pull all of these various systems together.
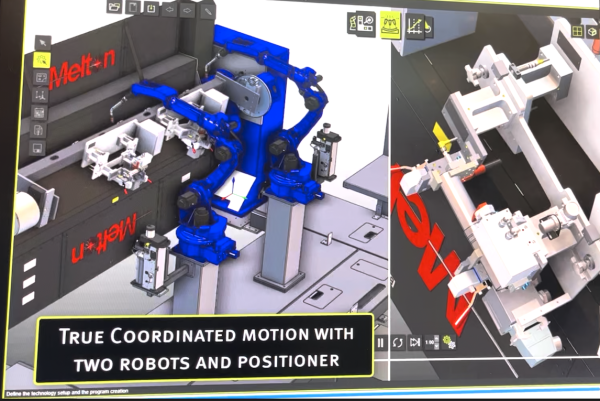
FastSuite aims at Simulating the Robotics/Welding process prior to going into production
While we’ve been disconnected from one another through the Pandemic, Manufacturers and Technologists alike were all able to gather in Chicago this September for a spectacular turnout at IMTS 2022. Exhibitors demonstrated an accelerated look into the future filled with Software-enabled production, Digitally-driven Manufacturing, and Equipment/Hardware to support our ever-evolving Global Supply Chain. It’s fascinating for me, who’s only been involved professionally in Manufacturing Technology for just 6 years to see such a vast evolution with everything, via the IMTS show. I’m ecstatic for 2024 and what it will bring, oh, and for FormNext to be in the Windy City in just 3 years!